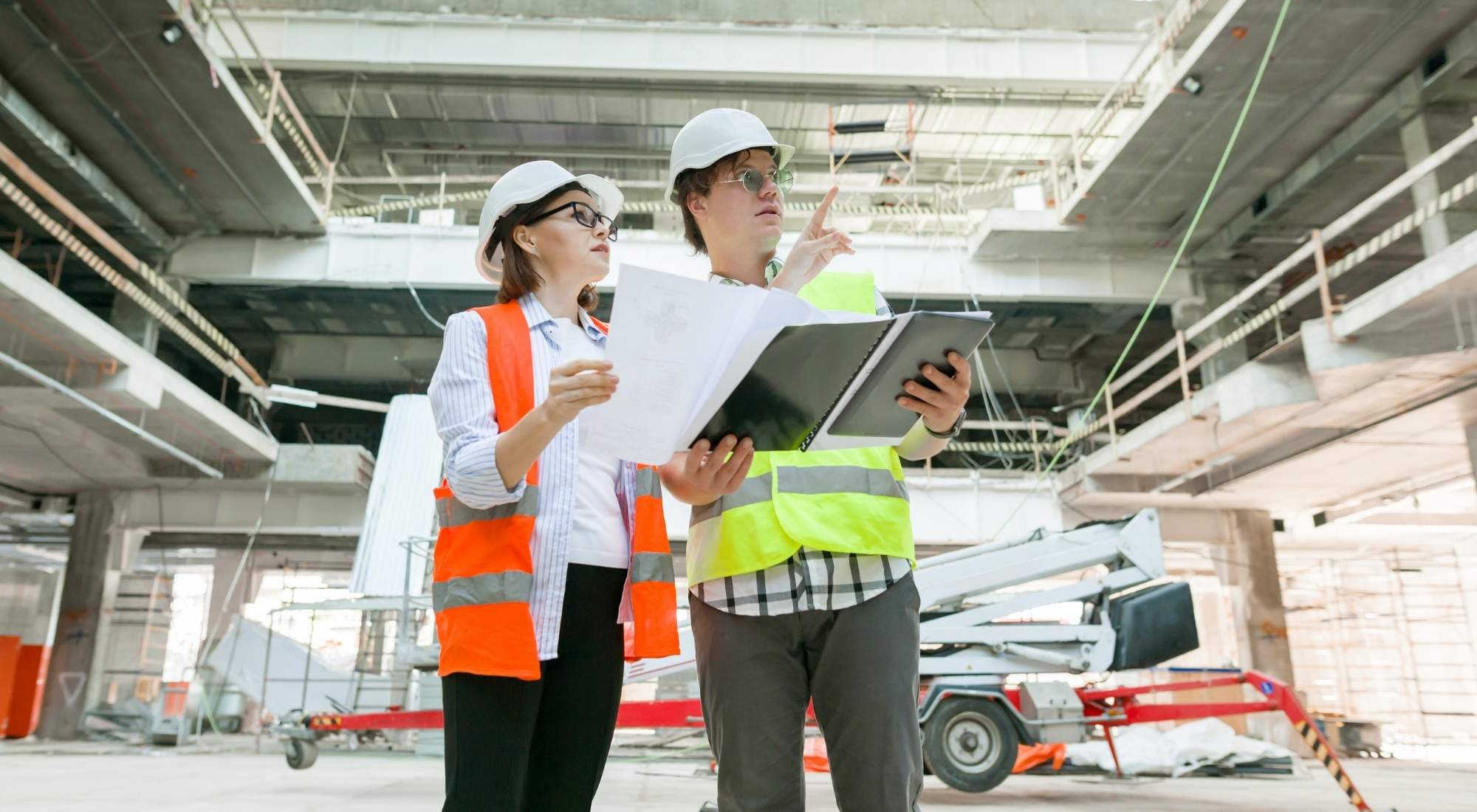
Your client has worked with a design team, drawing up their dream building, and can hardly wait for construction to get started.
While you were sure you would get this bid, the client is telling you that it's coming in way higher than they expected.
Here's where the process of value engineering can help.
If you're curious about the ins and outs of value engineering in building design and construction, read on.
This article outlines the process, as well as the benefits, so you’ll understand everything you need to know about value engineering in construction.
Track Expenses and Change Orders With Flexbase
Flexbase is a construction software that makes it easy to keep everyone on your project connected and updated throughout the value engineering process.
With the Flexbase app, you can quickly take care of:
- Project tracking
- Invoicing
- Applications for payment
- Legal reminders
- And much, much more
What Is Value Engineering in Construction?
It all started in World War II.
Lawrence D. Miles, a vacuum tube engineer for General Electric, was faced with shortages that made the usual materials unavailable. This started the wheels turning in Miles’ creative brain as he began the quest to find substitutes for the original supplies.
Not only did Lawrence find materials that were better than the originals, but they were also often less expensive.
Following the war, Miles developed the methodology of “value analysis,” or value engineering.
Value engineering in construction is a method that can be used by your project team to improve the value of your building project.
It involves examining the purpose of each element in the construction process, as well as its cost, with the goal of improving the functionality and keeping your cost as low as possible.
The process of value engineering in construction incorporates a team of engineers and designers who come together to critically analyze each step in the project to ensure maximum value.
After weighing the cost-benefit ratio, the team then presents ideas for alternate methods of …
- Construction
- Design; or
- Materials
… that will improve the value of the project.
It's important to note that improving the value of the project is not necessarily synonymous with cutting costs.
Instead, the goal is to optimize the elements of the project by analyzing all relevant factors, including:
- Cost
- Wear and tear
- Upkeep; and
- Aesthetics
In order for construction value engineering to be successful, it's critical that the construction and design team have a good understanding of the project as a whole, as well as the vision and goals for the project.
Benefits of Value Engineering in Construction
Employing value engineering in construction projects has multiple benefits, including:
- Cost reduction
- Quality improvement
- Increased customer satisfaction
- A simplified construction process
- Higher profit margins
- Better utilization of resources
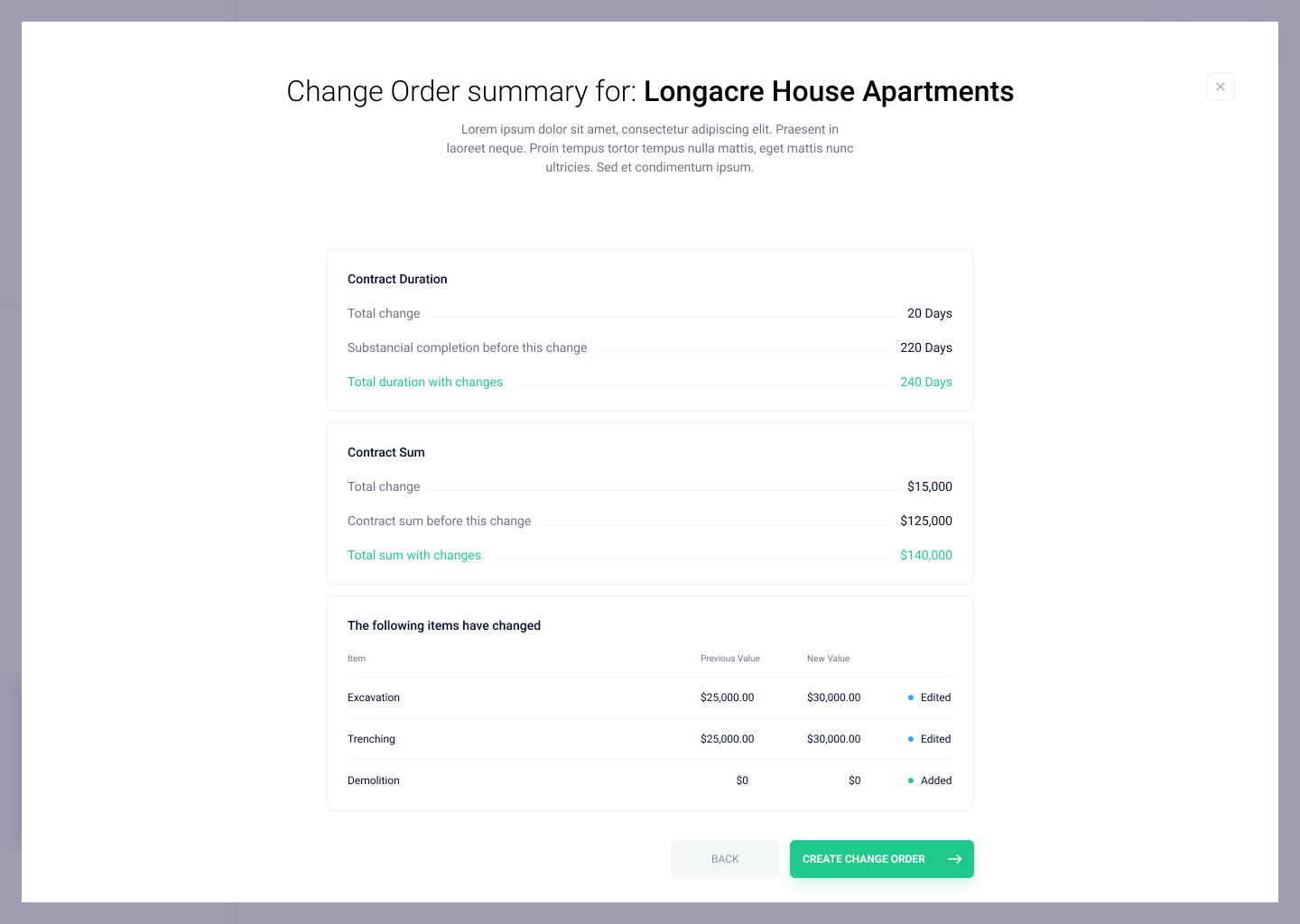
How Is ‘Value’ Defined in Construction?
In order to fully understand the process of value engineering in construction, you need to go beyond the upfront cost.
When assessing “value” in construction, you want to consider:
- Cost reduction
- Quality; and
- Maintenance
Cost Reduction
Reducing the cost of a project is the factor that drives many value engineering processes.
After analysis, the value engineering team will present ideas of less costly materials for you to consider.
This might look like pointing out a feature that may be unnecessary, or presenting a similar style of countertop that may cost less overall.
Quality
Cost reduction is a huge part of the overall process, but if you aren’t taking a close look at quality, you may be diminishing the value of your project.
When it comes to value engineering in building design and construction, quality factors into every part of the project, including the quality of the:
- Environment you are creating
- Products making up the environment; and
- Team working on the project
Sometimes, the importance of quality will trump cost, such as when the quality of a component justifies the purchase price.
Investing in items and elements that have a higher price tag may have a positive impact on the happiness and productivity of those who will be using the space you are creating.
In the long run, a high-quality product may have more overall value than one that costs less money.
Maintenance
Next on the list is maintenance.
As it was with quality, it's important to consider the long-term care of value engineering decisions in construction projects.
One of the value engineering examples in construction is that while you may be able to score a great price on flooring, if it has to be replaced twice as often as flooring that costs a bit more, you may wind up spending more money in the long run.
On the other hand, if the owner needs to save extra money on the front end, and it's critical to get your project off the ground, then the lower-priced flooring may very well be your best option.
How Is Value Engineering Calculated?
Value engineering of building services is calculated as the ratio of function to cost.
Value may be added to a project by cutting costs or by improving the function. Typically, companies use value engineering to cut costs while still preserving the basic function of the product.
What Are the 5 Phases of Value Engineering?
The 5 phases of value engineering in construction are:
- Information — Data-gathering
- Speculation — Generating ideas
- Evaluation — Judging and analyzing ideas
- Development — Selecting and expanding on promising ideas
- Presentation — Presenting ideas to the client
#1: Information Phase
The goal of the information phase of value engineering in construction is to pinpoint the:
- Material
- Makeup; and
- Scope of the project
The focus is on the facts alone.
During this phase, the value engineering team will gather data and study components such as the …
- Materials
- Construction schedule
- Costs
- Drawings; and
- Specifications
… of the project in order to get a clear understanding of the ins and outs.
An example of value engineering in construction during the information phase might involve collecting data such as:
- The location of the building
- Who will be using it
- What type of lighting is needed
- The area of town it is located in
- The finished “look” desired (contemporary, classic, retro)
- The hours of use for the finished product
- The internal components of the project such as offices, a boardroom, or a kitchen
#2: Creative Speculation Phase
During the creative speculation phase of value engineering, the team will brainstorm ideas for potential design solutions to help the project reach the required functions.
This phase is a judgment free-zone, with every viable option being included, even those that may have serious flaws.
The ideas presented during this time should be related to the information that was collected during the information phase and focused on lowering the initial costs and increasing value.
Every aspect of the life-span of the project should be taken into consideration, including:
- Safety
- Materials and tools needed
- Environmental factors
- The best type of foundation
- Analysis of the construction site
By the time the creative speculation phase is over, the team has ideally narrowed the problem down to two words — an open-ended subject and a verb.
For example: Say the project is a school building in northern Alaska, and you’re generating ideas for the subject/verb combo, “heat maintainer.”
Ideas tossed out may include:
- Face all the glass south
- No shade trees
- Use passive solar window glass
- Install a fireplace in every room; and
- Double the number of heating vents
#3: Evaluation Phase
Now it's time to assess the ideas and weigh one alternative against another.
Experts may be brought in to help define the feasibility of the possible options.
For example: A fireplace in every room? That's obviously not a viable option in a school building, but additional heating vents are a good possibility.
All ineligible ideas are tossed out during this process of elimination and when the evaluation phase is complete, only the strongest of the options will have survived.
The goal here is to determine how well each alternative can perform the set function of the original solution.
Details matter and the owner's original intention is kept at the forefront because to veer from that is to miss the mark, and possibly miss landing the contract.
#4: Development Phase
The development phase is next in the process of value engineering in building design and construction.
Here, each idea that made it past the evaluation phase is now put to additional tests, including ...
- Availability
- Pricing
- Long-term costs; and
- Required maintenance
… and the ideas that make the cut are the winners.
The remaining ideas are then turned into a proposal that will be presented at the final stage of the project.
The proposal incorporates …
- The pros and cons of a proposed solution
- Sketches
- Design models
- Cost comparisons
- A project timeline
… and any other information that would be helpful to the client.
#5: Presentation Phase
Finally, we arrive at the presentation phase of value engineering.
This is where you present your findings to the project owner.
For example — Adding passive solar windows is an added cost, but overall is less expensive than the amount of forced-air heating that will be needed to keep the students comfortable in sub-zero weather.
This phase provides an opportunity to explore the final possible alternatives, determining if the proposal is properly-suited to meet the needs of the project as it moves forward.
The goal of the presentation phase of value engineering is to obtain approval for the project.
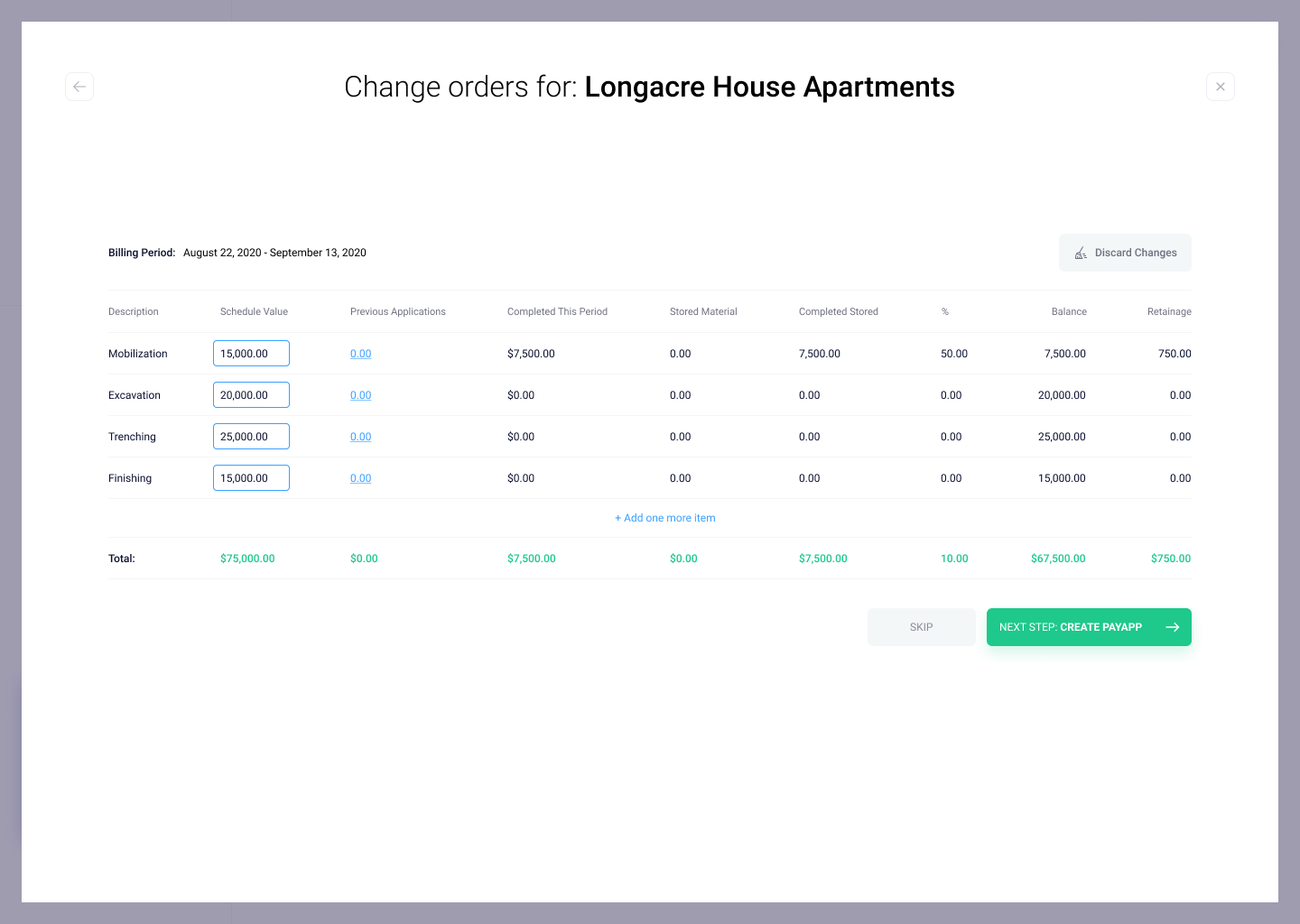
When Is the Best Time to Value Engineer?
Typically, the best time to do value engineering is during the planning stage of the project.
At that point, the cost of implementing any changes will be at its lowest and will have the least impact on the project’s schedule.
Though it can be applied during any phase of the design process, applying the methodology early will save time and costs down the line, providing a better return on investment.
Implementing value engineering during product planning may require more preparation upfront, but can potentially save you from costly change orders down the road.
Stay on Top of Value Engineering Changes With Flexbase
As a contractor, you understand the importance of value engineering in construction.
At Flexbase we take the hassle out of tracking your expenses and making it easy to execute any necessary adjustments with change orders.
Flexbase provides you with a streamlined automated payment process.
Let us take care of all the construction payment management steps for you, including:
- Project tracking
- Invoicing
- Legal reminders
- Applications for payment
- And much, much more
The Flexbase platform is able to fully integrate with the accounting and construction payment management software you already use, so your transition is seamless.
And what’s more, our resources are 100% free to use. You don’t pay us unless you get paid.
Schedule your free demo with Flexbase today to see how you can:
- Automate the change order process
- Get paid faster; and
- Avoid costly delays